Designed to work in tandem, the new machinery will allow Omega’s skilled toolmakers to make reliably accurate cuts, quickly and easily. Using the EDM drill, operators can cut through steel quickly to produce a hole as a starting point for the wire EDM to thread through to start the wire erosion process.
“Our new wire EDM allows us to achieve tighter tolerances, more complex shapes without distortion and also opens up our scope of work as we move more and more into fully-hardened production tooling,” said Steve Fairbairn, tooling manager at Omega Plastics.
“We have been using an older model Fanuc wire EDM for the past 19 years which has served us well, so we decided to stay loyal to the brand and purchase a new machine with the latest technology on board which provides us with more capacity in the X, Y and Z axes.
“By using the wire eroder in line with the new hole starter, we can also actively reduce the amount of waste metal we produce. Any offcuts are able to be reused for other tools because of the accuracy at which they have been cut, helping to improve the sustainability of our entire operation.”
The Omega Plastics Group provides a full-service turn-key solution from design, through to manufacturer, assembly and dispatch for its customer base operating across the automotive, FMCG, healthcare and building services sectors.
“The new kit we have installed at our Team Valley facility is fantastic,” added Craig Swinhoe, group managing director at Omega Plastics Group.
“The level of accuracy afforded by our newest pieces of equipment adds yet another string to our bow and will enable us to attract new, increasingly complex projects while also helping to drive our in-house efficiencies.
“We now have two fantastic facilities in the North East and an experienced team of highly skilled toolmakers, engineers and project managers who are ready to provide our customers with a high-quality service using the latest machinery and technology.”
As well as investment in new equipment, the Group has also made significant investment in its people since its strategic move to new premises in the Team Valley Trading Estate in Gateshead earlier in the year to both further develop its in-house apprenticeship programme and provide additional capacity.
The new site is enabling a new, more efficient way of working between the company’s tooling and moulding departments. Stationed next door to each other within the 45,000 sq ft facility, the engineers responsible for the plastic injection moulding of Omega’s products are able to liaise closely with toolmakers to ensure high levels of efficiency and right-first-time orders on behalf of customers.
“The layout of our new facility at Team Valley provides a very fluid way of working for our toolmakers and engineers,” Dave Crone, executive chairman at Omega Plastics Group commented.
“Being able to handle both the tooling and moulding aspects of multi-use, sustainable plastic products under one roof has always been one of our key selling points. It simplifies the process and reduces risk to our customers, whilst accelerating their time to market through a cohesive approach to Design for Manufacture knowledge and supply chain management, providing total manufacturing control.
“We make it, we mould it, we assemble it, we deliver it”.
Combining the first-class design, tooling, moulding and assembly of Omega Plastics with the specialist high volume moulding provided by its sister company, Signal Plastics, Omega Plastics Group is one of the region’s leading providers of plastic injection moulding and specialist tooling services.
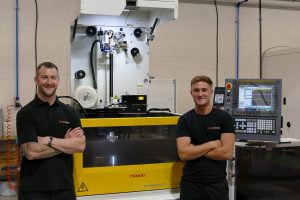